In focus: Electrolyser producers and start-ups
“The case to innovate in the field of electrolysis to make green hydrogen or oxygen is compelling. CAPEX costs must fall, operability must improve, and efficiencies must increase,” says Stephen B. Harrison of sbh4 consulting.
New technologies are emerging. Start-ups are blossoming and manufacturing heavyweights are turning their attention from traditional products to electrolyser production.
How will this help green hydrogen production? Will all these players make it through to the end game? Will safety issues shake out some less experienced operators?
These questions – and many more besides – are all addressed in the forthcoming Hydrogen Building Blocks training modules from Class of H2, and discussed here in this short read.
Innovation in alkaline electrolysis
Alkaline electrolysis is perceived as mature. The technology itself has been deployed at more than 100 MW scale for almost a century. However, new variants and stack designs are being developed that are less mature.
Start-ups and new, inexperienced electrolyser producers are also entering the market. For these players, even if they are working with a mature technology, there will be teething troubles and learnings before they are producing commercially mature products with high bankability level.
Harrison explains that “the diaphragm in an alkaline electrolyser is porous and there is a chance that oxygen and hydrogen gases can pass through it and create an unsafe explosive gas mixture. The risk of this is especially high when the electrolyser turns down to a low percentage of its maximum operating power input.”
“When premium materials are used, an alkaline electrolyser can operate at only 10% or 30% of its nominal power. On the other hand, if lower cost materials are selected the turndown may be limited to 50%. Alignment of this turndown with the renewable power feed profile is essential.”
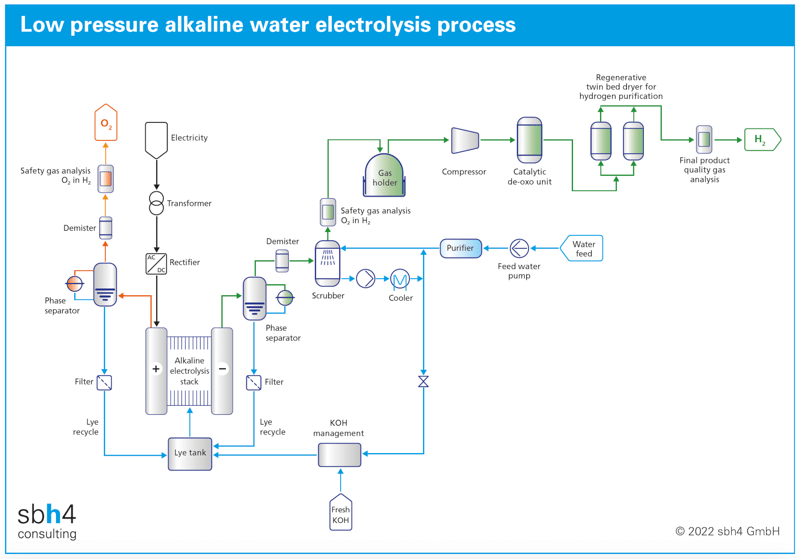
©sbh4 consulting
A further issue with turn-down on alkaline electrolysers is the recirculation of lye around the stack. This transports electrons through the system. If the electrolyser is shut off too rapidly, the surge of electrons can reverse and corrode the electrodes. It is like cars driving down the motorway: if one brakes, or goes into reverse suddenly, the implications are catastrophic.
Combatting the issue of ‘shunt currents’ and reducing the risk of electrode degradation can be achieved by using thicker and more expensive materials to coat the electrodes with the associated CAPEX penalty.
Shunt currents can also be mitigated by ensuring that a small, circa 10%, safety current continues to flow to the electrolyser. In an intermittent operating scenario, this would represent an opex penalty or require additional CAPEX for batteries to ensure a continuous power supply.
In addition to established and emerging producers needing to grapple with these fundamental aspects of alkaline electrolysis, there are breakthrough technologies on the horizon, such as the bubble-free capillary electrolysis under development by Hysata in Australia.
“At sbh4 consulting, I maintain a data base of electrolyser producers, stack builders, systems integrators and start-ups that are pre-production,” says Harrison. “The largest share of the pie, when we look at the range of technologies, is taken up by alkaline electrolyser producers, systems integrators and start-ups focusing on this technology.”
Progressive development of PEM electrolysis
PEM electrolysers can align well with variable renewable power and intermittent operation. There is a fundamental technical reason for this since the PEM membrane is less permeable than the diaphragm in an alkaline electrolyser. Also, in a PEM catalyst coated membrane assembly, a recombination catalyst layer can be included in the cell architecture to convert the potentially explosive hydrogen mixture to harmless water.
“The manufacturability of PEM electrolysers hinges on the ease of producing the MEA,” confirms Harrison. “Starting with a polymer sheet and painting catalyst soups onto it is one way. However, smarter ideas exist and have been implemented by the new generation of PEM producers. We can see the implications in the low stack costs they are offering. Productivity in the factory has taken a step change for the better.”
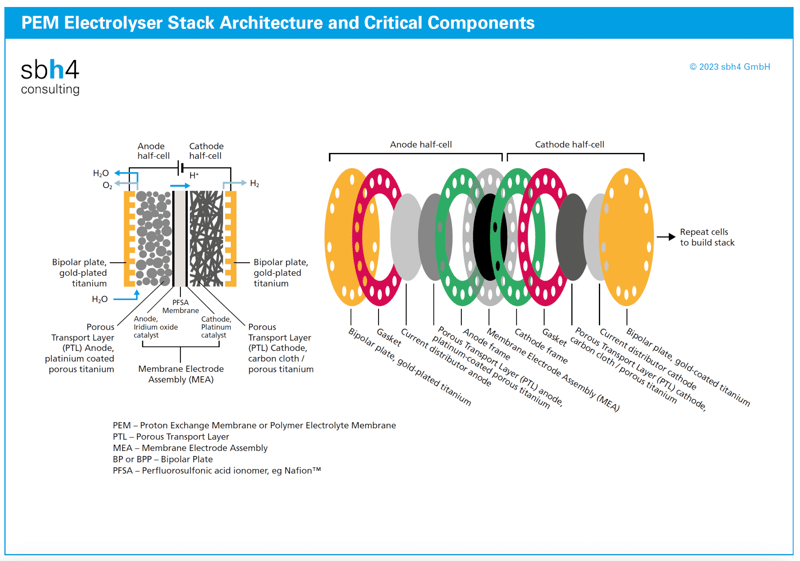
©sbh4 consulting
Building the membrane electrode assembly (MEA) for a PEM electrolyser is one of the most sophisticated manufacturing processes in the world of green hydrogen. What may appear to be a thin film of plastic, can contain five layers of polymer and catalyst coatings with different functionality.
“Despite the complexity, new PEM electrolyser system producers, or PEM stack builders are emerging at an astonishing rate,” Harrison adds. “The sbh4 database is frequently in need of updating to keep track of the new entrants in this technology group.”
AEM – challenging the green hydrogen paradigm
Green hydrogen and ammonia from hydropower was deployed at 100 MW-scale on large dams in Egypt, Norway, and Zimbabwe more than 50 years ago. These schemes operated atmospheric pressure and pressurised alkaline electrolysers on a continuous basis.
However, the intention to use variable wind and solar power and the idea of intentional intermittent operation to exploit negative priced power at times when renewables are flooding the grid have become important concepts for green hydrogen production.
One high-potential electrolyser technology that may align well with these operating regimes and business models is called AEM due to the use of an anion exchange membrane.
“When I started the electrolyser players data base at sbh4 three years ago, there was only one AEM player. Now there are about 15. AEM has gained momentum, it is being propelled into the major league of green hydrogen electrolysis technologies by many credible OEMs such as Enapter in Germany and high potential start-ups such as EVōLOH in the US,” says Harrison.
“However, it is important to differentiate between technology maturity, or TRL and commercial maturity known as CRL or commercial readiness level or bankability. Furthermore, manufacturability of MRL is key to achieving scale up and low-cost equipment.”
An advantage that the AEM technology offers is the use of commonly available, low-cost, earth-abundant materials for its construction. The membrane can be made of a fluorine-free polymer to avoid the issue of ‘forever chemicals’ and persistent soil and water pollution.
“Not all AEM producers are yet offering bankable solutions, and not many are yet working with scale production,” says Harrison. “But we are not far off achieving those milestones with this technology and I expect to see AEM challenge PEM in many GW-scale green hydrogen projects at the end of this decade.”
High-efficiency solid oxide electrolysis
Whilst AEM offers the attraction of alignment to intermittent operation, solid oxide electrolysis (SOEC) is a challenger technology that can achieve remarkably high efficiency when converting green electrons to green hydrogen.
At a system level, SOEC integrates perfectly into hydrogen derivatives projects since heat from downstream reactions such as ammonia synthesis, methanol production and Fischer Tropsch fuels can be used to pre-heat water for the high temperature SOEC operation. Under this operating mode, SOEC can offer between 20 and 25% efficiency benefits versus established alkaline and PEM technologies.
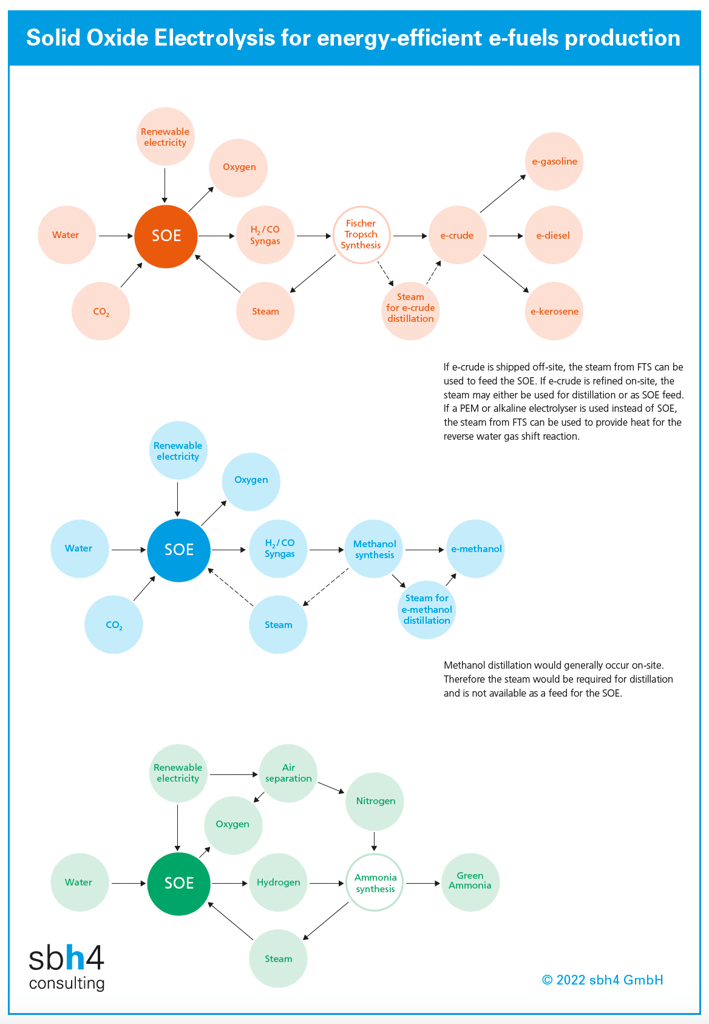
©sbh4 consulting
At present, the high CAPEX and low bankability of SOEC is holding it back. It has not yet been deployed at more than 10 MW scale. However, there are some project developers that are looking to integrate a small amount of SOEC electrolysis capacity into their electrolyser parks on a demonstration basis. These events will transform the future of SOEC electrolysis.
Many of the solid oxide electrolyser producers entered the market from their foundation building solid oxide fuel cells. Bloom Energy and Fuel Cell Energy, both in the US are good examples of companies that have made and are making this transition. In Europe, Ceres Power and Sunfire have taken a similar route.
“I believe that the technical challenges of building a high-temperature solid oxide stack will limit the number of entrants and long-term players in this technology,” confirms Harrison. “Despite the hurdles that must be jumped, we track around 15 solid oxide electrolyser producers. Some are focusing on stacks, others full systems.”
The overview
The merits of the challenger electrolyser technologies such as AEM and SOEC will be discussed during the forthcoming Class of H2 training, which Harrison will deliver on behalf of H2 View. Business models for large-scale deployment of PEM and alkaline electrolysers will also be presented.
Running green hydrogen projects with ammonia as the target molecule is also a mainstream concept. The technologies beyond electrolysis that are required to convert hydrogen to this flexible energy vector are also on the agenda in the forthcoming on-line training sessions.
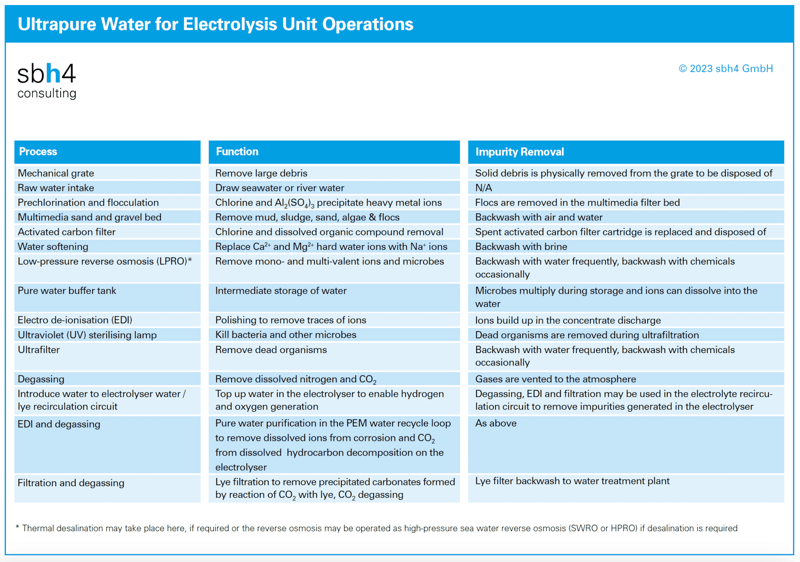
©sbh4 consulting
Ultra-pure water supply, water and lye management within the electrolyser and desalination are critical issues for successful electrolyser operation. The operational and safety risks grossly outweigh the costs of suitable technologies in these areas. Harrison will explain how to achieve the appropriate water quality specifications from tap water and sea water. He will also discuss the use of water for cooling electrolysers and alternative thermal management regimes that can minimise water consumption in arid regions.
The full database list of electrolyser producers can be purchased separately from sbh4 consulting to accompany and maximise the upcoming Class of H2 training. It is an invaluable market research resource for those who are seeking to address these companies and follow the progress within this dynamic sector.
Get up-to-speed on hydrogen with Class of H2
At a time when hydrogen is the new gold rush for so many investors and start-ups alike, and the skills gap risks becoming the skills gulf, H2 View’s Class of H2 presents a series of hydrogen training modules.
Our first masterclass is created to bring your hydrogen fundamentals up-to-speed, covering the basics, e-fuels and ammonia, low-carbon and green hydrogen production, turquoise hydrogen production, biomass pathways, and underground hydrogen storage.
To book your on-demand training session, click here. Or you can reach out to the Class of H2 team at +44 1872 225031 or [email protected].