Port-side ammonia crackers: Enabling international hydrogen supply chains
Before air separation and liquid nitrogen became prevalent, ammonia cracking was used to produce small amounts of nitrogen.
Small-scale ammonia cracking will be required in the future in advanced energy systems to convert ammonia into hydrogen at the point of use. Liquid ammonia is easy to store and transport due to its high energy density. And it can conveniently be cracked back to hydrogen on-demand.
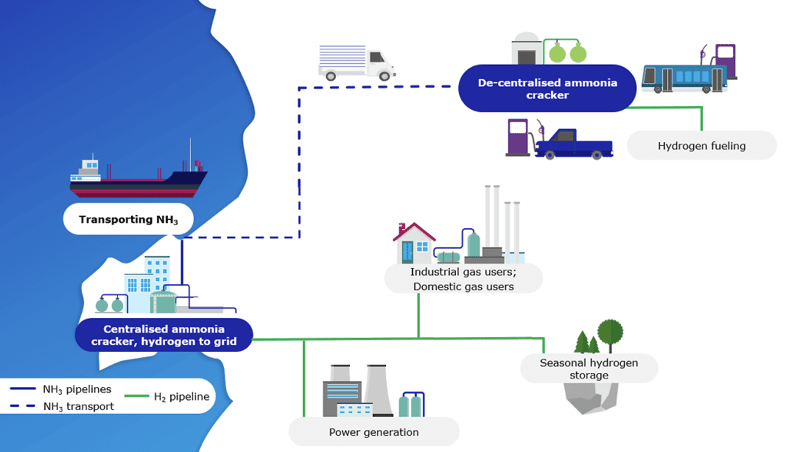
©Johnson Matthey
On-demand, decentralised hydrogen generation
Priyan Mistry, Business Development Manager, Ammonia Cracking Technology & Catalysts at Johnson Matthey, explains that “cracking ammonia is not a new process, but up until now, it has been carried out on a relatively small-scale.”
“To start up an ammonia plant,” continues Mistry, “a small amount of hydrogen is needed as a utility to get the recycles going, for purification purposes, to help with the burner systems, and to activate the catalysts.” This hydrogen can be produced from a small electrically heated cracker and, once the plant is up and running, the ammonia plant can provide large sources of hydrogen. In application, these small, electrically heated ammonia crackers are only used for short periods.
To support both small and large-scale crackers, JM has two discrete categories of catalysts. “For smaller-scale, distributed ammonia cracking systems, JM has developed a platinum group metal catalyst,” says Mistry. This high-activity catalyst operates at temperatures between 400-500°C. JM supplies this catalyst to OEMs who integrate it into their technology to create an efficient solution for small-scale cracking systems.
Low-carbon production for export
Green ammonia is produced from green hydrogen, which is generated through the electrolysis of water using renewable power. The Helios project in NEOM is the largest green ammonia project under construction. It will create up to 600 tonnes of carbon-free hydrogen of ammonia for export to locations such as Germany.
Blue ammonia can be produced at scale in countries with abundant stranded natural gas reserves where there is also the possibility of underground geological carbon dioxide (CO2) sequestration. Several export-oriented projects have been proposed in the US Gulf Coast where these conditions are met.
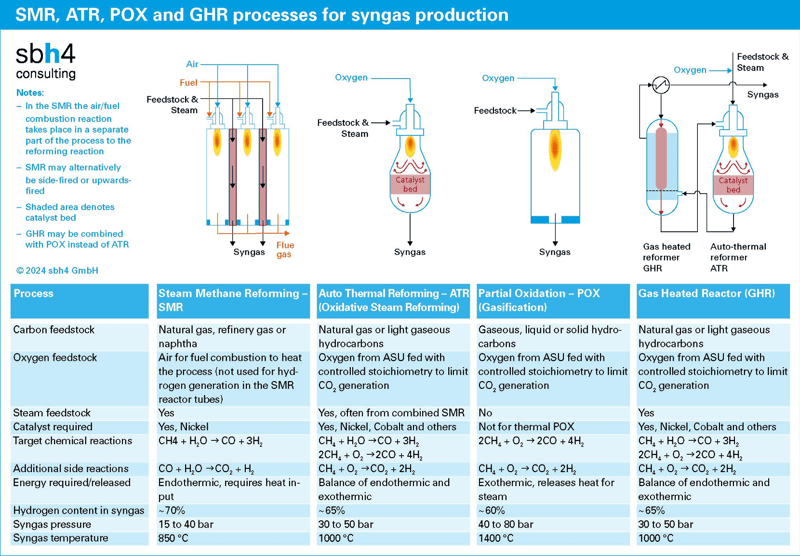
©sbh4 consulting
The technologies to produce blue ammonia are based on steam methane reforming (SMR) and other variants of this reforming process that have been used for decades to make grey ammonia or methanol. However, when making blue ammonia, the requirement to capture CO2 at pressure for underground injection favours the use of Auto Thermal Reactors (ATR), Partial Oxidation (POx) and Gas Heated Reactors (GHR).
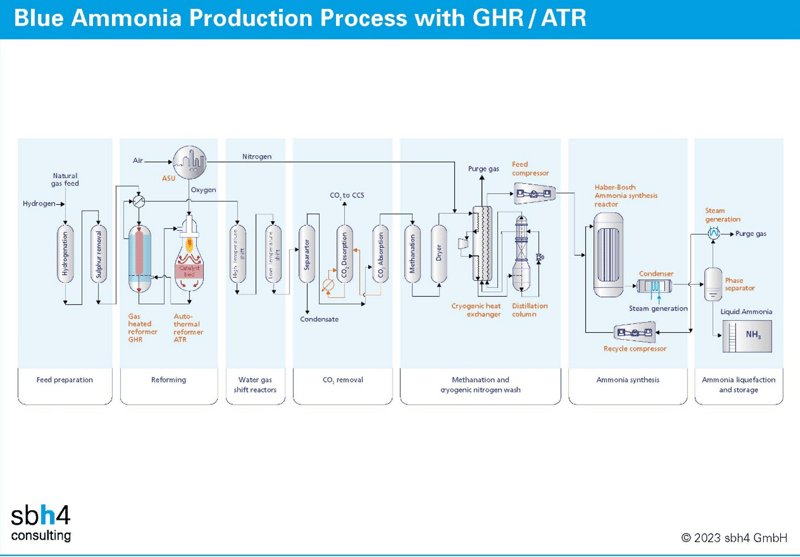
©sbh4 consulting
Ammonia trade and terminals
Import infrastructure is also being expanded. On the North Sea coast of Germany, Brunsbüttel and Hamburg have been earmarked as potential locations for new ammonia terminals. In the Netherlands, Rotterdam and Vlissingen are also building and refurbishing ammonia terminals.
Large, port-side ammonia crackers will also be used to convert imported, clean ammonia to hydrogen for distribution by pipeline. The high volumetric energy density of liquid ammonia and the maturity of shipping and terminal infrastructure mean that ammonia is poised to ramp up rapidly as a clean energy vector to link low-cost producers with importers.
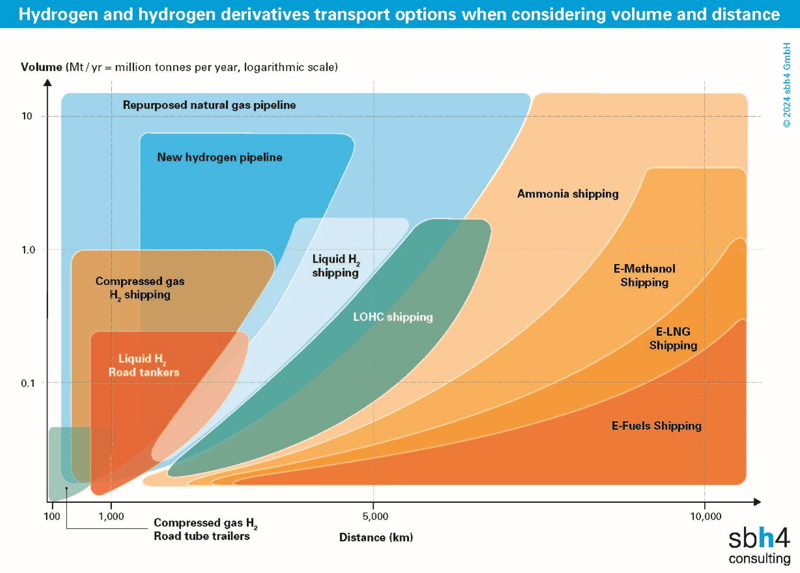
©sbh4 consulting
Continuous ammonia cracking at scale
“When it comes to centralised, large-scale crackers, the high cost of platinum group metals quickly makes them a prohibitive option,” says Mistry. For these systems, JM has sold nickel-based catalysts for electrically heated applications for decades which, although they do not have the same level of activity as the platinum group metal catalysts, are robust enough to withstand the very high operating temperatures (600-800°C). This temperature is required to produce the necessary high levels of efficiency from centralised ammonia crackers.
In the case of large-scale ammonia cracking, JM has developed a complete technology package, which includes supply of the appropriate catalyst. The process and technology is synergistically designed around the catalyst, enabling greater optimisation of overall process and improved efficiency.
Ports and terminals are anticipated to be key locations for ammonia crackers. For example, they will be deployed in ports and terminals to convert large volumes of imported ammonia into hydrogen which can be used to generate electricity or will be distributed through pipelines to end-users.
Ammonia cracker plant design
A large-scale ammonia cracker is akin to a traditional steam methane reformer that produces much of the world’s hydrogen today. The cracker at the heart of the process flow sheet consists of a large, top-fired, furnace. This is a hot-box with alternating rows of catalyst-filled tubes and burners. The burners provide heat into the flue duct, which is then transferred into the catalyst tubes where the reaction takes place.
The JM ammonia cracker uses a small amount of ammonia feedstock, which is blended with waste gases from the process before being fed to the burners to drive the cracking reaction. This offers a way to fire the system without producing carbon emissions or using hydrogen product as a fuel. “By using ammonia instead of the hydrogen product from the cracker, the size, cost, and efficiency of the system can be optimised,” says Mistry.
Excess heat which is produced from the burners is recovered from the flue gas for beneficial use, such as process heat recovery and steam generation. An abatement control system is also used to clean the flue gas before it is released to the atmosphere. JM is a leading provider of DeNOx and other emissions control technologies, and abatement control systems are within their scope of supply.
Minimising carbon intensity
The JM ammonia cracker is designed to minimise the capital cost, footprint and ammonia consumption. “The core motivation for producing blue or green hydrogen and low-carbon intensity ammonia is to replace carbon-emitting fossil fuels in certain applications,” says Mistry. “So, the JM process is also designed to minimise carbon intensity of ammonia cracking.”
The potential to decarbonise would be reduced if natural gas were to be used to fire an ammonia cracker. Hydrogen product could also potentially be used, but this would require a greater hydrogen production level, which equate to a higher capital cost due to the need for a larger system.
Ensuring system efficiency
The other important parameter is efficiency, i.e. the volume of hydrogen produced against ammonia consumed. This is a significant factor as a higher efficiency process will help to minimise the levellised cost of hydrogen. The cost of the hydrogen produced is a critical factor for this new energy, both in terms of what people are willing to pay and, of course, financial investment decisions.
By using ammonia to fire the cracker, the JM design simultaneously minimises capex, opex and the carbon intensity of operation. JM has long experience in ammonia cracking – nearly 100 years. Mistry concludes by saying that “our knowledge of catalysts combined with proven experience in large system design and scale-up have supported the creation of an ammonia cracking system that offers cost-effectiveness, efficiency, and reliability.”
Decarbonisation Summit 2024: Industrial Gases and Clean Energies 3.0
The global industrial gas and equipment business has an imperative role to play in the future of clean fuels and decarbonisation. The energy transition simply won’t happen without it.
At the same time, the industry has its own activities to decarbonise and circular economies to carve out – think green air gases and bio-based carbon dioxide (CO2), as well as CO2 utilisation and e-fuels, and so much more besides.
There are pathways to progress and questions to answer on this journey, not least:
- What are the compelling clean fuels and what do the pathways to production look like?
- How can the gases industry participate in this playground of opportunities?
- What can other alternative fuels mean for the CO2 industry and its stakeholders?
These questions and more will be in the spotlight at gasworld’s Decarbonisation Summit in April 2024. To attend, sponsor and for more information, visit https://bit.ly/GWDECARB-S24