ASCO Carbon Dioxide Ltd: Then and now
This October gasworld celebrates its 20th anniversary, charting key moments, events and industry stakeholders over our last two decades.
It’s been a progressive period of activity marked by multiple milestones and product launches, but it’s also been a timeline of rapid advancement in technologies and various sectors of the industry.
The business of carbon dioxide (CO2) and dry ice has been one of the biggest and fastest-growing spaces across this timeframe, with a range of new and expanding end-user markets, a number of supply chain shortages, and a shift in perception from a ‘nasty’ greenhouse gas (GHG) to an invaluable product in its own right and a key component in the drive for decarbonisation.
Against this backdrop, new names have emerged in the CO2 and dry ice sector, while others have endured through challenges and windows of opportunity.
One such established force that has truly stood the test of time, is ASCO Carbon Dioxide Ltd.
Now in business for more than 45 years, the company has both witnessed and been at the forefront of all aspects of evolution in the CO2 value chain – and here we look back at the company’s own development over recent decades.
Then…
In 1975, Thomas Trachsel laid the foundation for the today’s company, ASCO Carbon Dioxide Ltd. Initially, ASCO solely focused on filling and delivering CO₂ in gas cylinders for the Swiss beverage industry. However, through a combination of determined entrepreneurship and excellent customer service, ASCO gradually expanded its expertise and offerings in the field of CO₂ applications over the years.
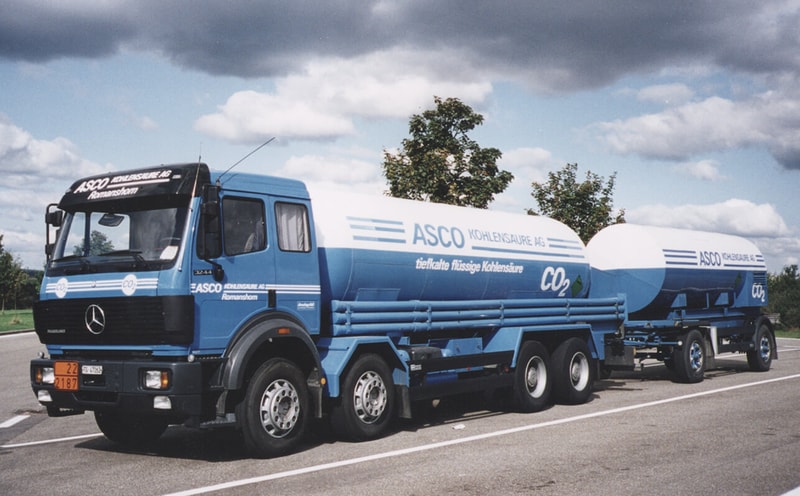
©ASCO Carbon Dioxide Ltd
The company ‘Carbonic Industries’ from New Zealand proved to be the ideal partner for a large-scale entry into the CO₂ market. ASCO took over the international representation of the entire product portfolio for carbon capture plants and embarked on an impressive expansion journey.
In 1987, Carbonic Industries was integrated into ASCO, and ASCO became one of the leading providers of carbon capture plants worldwide. The CO₂ market continued to grow, and in 2005, ASCO expanded its product range. With ‘Diffusion Hydraulique S.A.R.L.’ acquisition, another company and a manufacturer of dry ice production machines joined the ASCO family to build expertise in the dry ice sector.
Another milestone in ASCO’s history was achieved in 2007, when the company joined the Messer Group and took over the role of the CO₂ competence centre within the globally operating, family-owned industrial gases conglomerate.
In pursuit of continually expanding expertise in the field of CO₂ applications and following a long and highly successful partnership with the Swiss company Remco AG, a specialist in dry ice blasting equipment, the company was acquired in 2011. Since then, dry ice blasting technology has become one of ASCO’s core competencies. In 2014, BUSE Gastek and ASCO Carbon Dioxide Ltd. decided to join forces in the field of CO₂ processing and dry ice technology, resulting in a significant merger that allowed ASCO’s expertise in dry ice technologies to grow to over 130 years in total.
In 2016, ASCO ventured a further step forward and founded its North American subsidiary, ASCO Carbon Dioxide Inc. headquartered in Jacksonville, Florida.
In more recent years, ASCO has increasingly extended its product portfolio, especially in the field of dry ice production, packaging and handling solutions.
Due to new market demands that can be traced back to the Covid-19 pandemic, where high capacity pelletizers and handling technologies as well as new business models such as temporary rental solutions were needed, ASCO constantly drives innovation. A dedicated team develops digital technologies, with pelletizers now benefiting from standard remote support and remote monitoring.
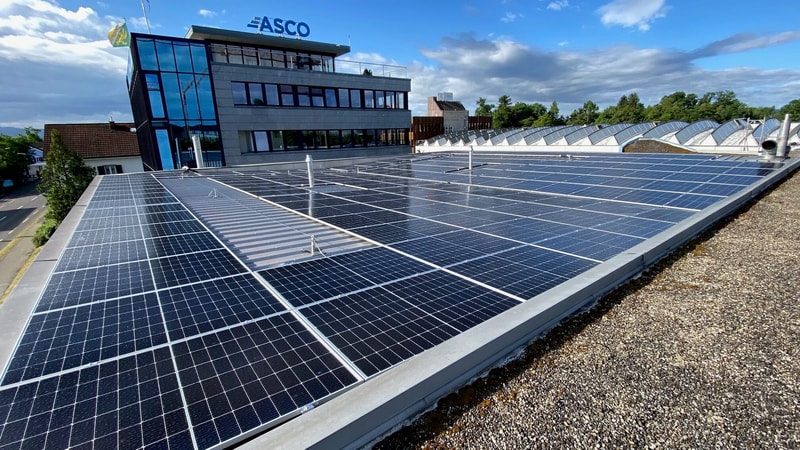
©ASCO Carbon Dioxide Ltd
Now…
ASCO Carbon Dioxide Ltd is one of the leading providers in the fields of carbon capture plants, as well as dry ice production and blasting technology.
With a combined more than 100 years of history and commitment to innovation, quality, and sustainability, ASCO Carbon Dioxide Ltd. has become a reliable partner for companies worldwide.
The success of ASCO Carbon Dioxide Ltd. can be attributed to its core competencies, which extend to three main areas:
- Carbon capture plants – One of the main strengths of ASCO Carbon Dioxide Ltd. lies in its advanced CO₂ recovery systems. These systems differ based on the sources of CO₂.
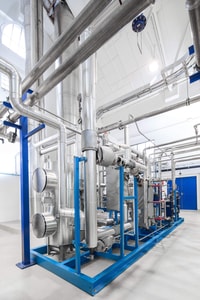
©ASCO Carbon Dioxide Ltd
The groundbreaking ASCO CO₂ Stack Gas Recovery System (SGR), turns the vent flue gas into a usable and profitable source of CO2. This gas secured by an ASCO SGR System is a by-product of flue gas production from boilers, as well as from other flue gas sources, offering an economic CO₂ source to any CO₂ consumer or reseller. ASCO, as a provider of complete CO₂ solutions, offers CO₂ Stack Gas Recovery Systems with various capacities.
The innovative ASCO CO₂ By-Product Recovery (BPR) turns the vented by-product gas into profitable CO2. Whether for an alcoholic fermentation process (breweries, ethanol operations, distilleries or wineries), other industrial sources (ammonia production or hydrogen reforming) or natural sources, ASCO will find your individual CO₂ recovery solution.
The ASCO CO₂ Gas Revert Recovery System (RRSi) is designed to recover the CO₂ gas returning from ASCO Dry Ice Pelletizers and reintroduce it into the dry ice production process. This process results in a conversion rate of 90-95 %.
- Dry ice production – Dry ice (solid CO₂) is a versatile substance used for various applications such as cooling, shipping, and industrial processes, including dry ice blasting. Custom designing complete dry ice production centres has been a core competency of ASCO Carbon Dioxide Ltd. for decades. The portfolio includes not only standardised products, but ASCO also designs and customises these machines to meet individual customer requirements.
With the continuous development of the dry ice market, the demand for automated dry ice production centres has significantly increased, and customers worldwide are seeking customised solutions for their dry ice logistics.
- Dry ice blasting technology – Dry ice blasting is a cleaning method that utilises dry ice to remove contaminants from surfaces. Key aspects of this technology include that contaminants are removed gently as it doesn’t involve abrasive media or chemicals; dry ice is environmentally-friendly, producing no waste as it sublimates upon impact; that it is non-conductive and can be used to clean electrical components and equipment.
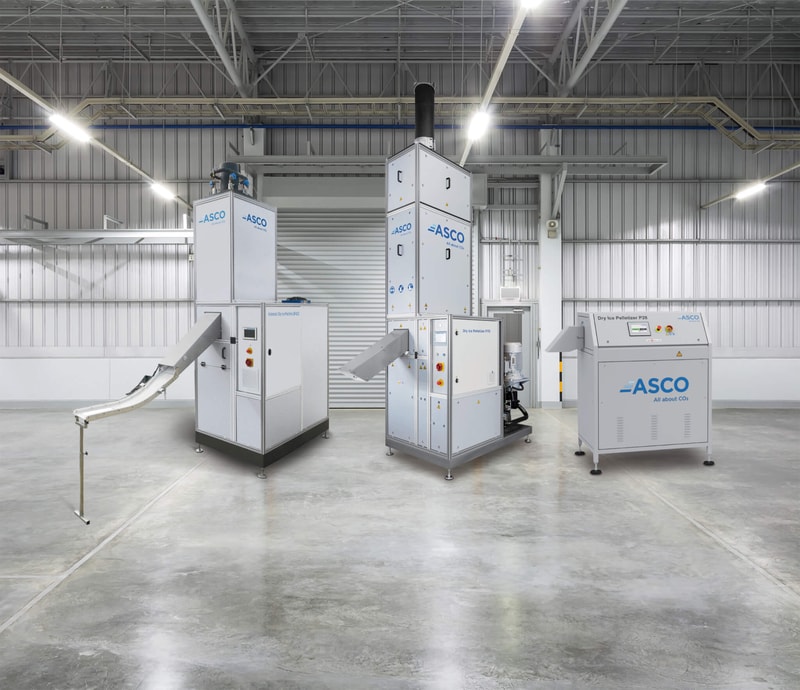
©ASCO Carbon Dioxide Ltd
Tomorrow: Helping to reach climate goals
Having considered then and now, what about tomorrow and what the future holds?
At a time when sustainability is a growing concern for companies worldwide, ASCO Carbon Dioxide Ltd. is committed to playing its part in reducing environmental impact. By promoting state-of-the-art carbon capture utilisation and storage (CCUS) solutions, the company supports global efforts to reduce CO₂.
In fact, ASCO actively strives to minimise its own ecological footprint through the implementation of eco-friendly initiatives like solar power and the optimisation of production processes.
Tomorrow: Continuous evolution, globally
ASCO Carbon Dioxide Ltd’s global presence is evidence of the company’s commitment to serving customers worldwide.
With a network of subsidiaries and strategic partners, the company ensures that its industrial gas solutions are accessible to businesses around the world. This global reach allows ASCO Carbon Dioxide Ltd to provide timely and efficient solutions regardless of the geographical location.
In a world marked by industrialisation and innovation, ASCO has carved a niche as a reliable and forward-looking provider of industrial gas solutions. With a rich history dating back to 1900, the company has continuously evolved to meet the dynamic demands of the industry. Its core competencies in carbon capture, dry ice production, and blasting technology have solidified its position as an industry leader.